Forskare inom EU:s Graphene Flagship rapporterar nu om en ny metod för att integrera grafen och 2D-material i tillverkningsprocessen för halvledare – en milstolpe hävdar forskarna inom det nyligen lanserade europeiska projektet 2D-EPL. Resultaten finns publicerade i Nature Communications och en av huvudförfattarna till artikeln är Arne Quellmalz från KTH.
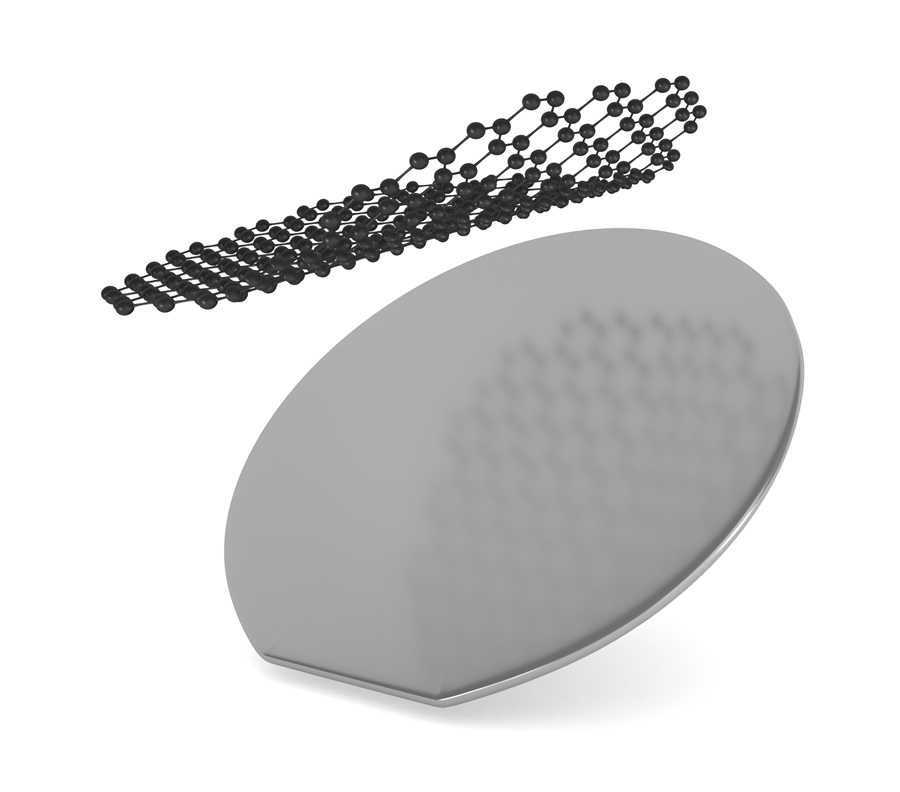
Forskare inom Graphene Flagship rapporterar nu om en ny metod för att integrera 2D-material i tillverkningslinor för halvledare.
Grafik: A. Quellmalz, KTH
Tvådimensionellt (2D) material förväntas ha en enorm potential för att utveckla enheter som är mycket mindre och som kan erbjud fler funktioner än vad som kan uppnås med dagens kiselteknik. Men för att utnyttja denna potential måste vi kunna integrera 2D-material i tillverkningslinorna för halvledare – ett notoriskt svårt steg. Ett team med Graphene Flagship-forskare i Sverige och Tyskland rapporterar nu om en ny metod för att få detta att fungera.
Tekniken, har publicerats i Nature Communications av forskare från Graphene Flagship-partners såsom RWTH Aachen University, Universität München och AMO GmbH, i Tyskland, Graphene Flagship Associate Member Kungliga tekniska högskolan (KTH) i Sverige, och i samarbete med Protemics GmbH.
Integrationen av 2D-material med kisel eller med ett substrat med integrerad elektronik medför ett antal utmaningar.
– Det finns alltid det här kritiska steget med överföringen från ett speciellt tillväxtsubstrat till det slutliga substratet som man bygger sensorer eller komponenter på, säger Arne Quellmalz, forskare på Graphene Flagship Associate Member KTH och huvudförfattare till artikeln. Du kanske vill kombinera en fotodetektor i grafen för optisk kommunikation med ”read-out”-elektronik i kisel, men tillväxttemperaturen för dessa material är för hög, så du kan inte göra det direkt på enhetens substrat.
Hittills är de flesta av de experimentella metoderna för överföring av 2D-material från dess tillväxtsubstrat till önskad elektronik antingen icke-kompatibla med högvolymtillverkning eller leder till en signifikant nedbrytning av 2D-materialet och dess elektroniska egenskaper. Skönheten i lösningen som föreslås av Quellmalz och hans medarbetare är att den finns i de befintliga verktygslådorna för halvledartillverkning: att använda ett standard dielektriskt material som kallas bisbenzocyklobuten (BCB), tillsammans med konventionell waferbindningsutrustning.
– I princip limmar vi ihop de båda skivorna med ett harts bestående av BCB. Vi värmer upp hartset tills det blir visköst, som honung, och trycker 2D-materialet mot det. Vid rumstemperatur blir hartset fast och bildar en stabil anslutning mellan 2D-materialet och wafern. För att stapla material upprepar vi stegen för uppvärmning och pressning. Hartset blir visköst igen och beter sig som en kudde eller en ”vattensäng” som ger stöd till lagerstapeln och anpassar sig till ytan på det nya 2D-materialet. säger Quellmalz.
Forskarna demonstrerade överföringen av grafen och molybdendisulfid (MoS2), som en representant för transition metal dichalcogenider, och staplade grafen med hexagonal bornitrid (hBN) och MoS2 till heterostrukturer. Alla överförda skikt och heterostrukturer var enligt uppgift av hög kvalitet, det vill säga, de uppvisade en enhetlig täckning över en upp till 100 millimeter stor kiselskiva och uppvisade en låg belastning hos de överförda 2D-materialen.
– Vår överföringsmetod är i princip tillämplig för alla 2D-material, oberoende av storlek och typ av tillväxtsubstrat. Och eftersom det endast är beroende av verktyg och metoder som redan är vanliga i halvledarindustrin kan det väsentligt skynda på introduktionen på marknaden för en ny generation enheter där 2D-material är integrerade ovanpå konventionella integrerade kretsar eller mikrosystem. Detta arbete är ett viktigt steg mot detta mål, och även om många andra utmaningar kvarstår så är utbudet av potentiella applikationer stort: från fotonik, till avkänning, till neuromorf databehandling. Integrationen av 2D-material kan vara en riktig ”game-changer” för den europeiska högteknologiska industrin, säger professor Max Lemme, från Graphene Flagship-partner AMO GmbH och RWTH Aachen University.
Nyligen inledde Europeiska kommissionen ett projekt på 20 miljoner euro för att överbrygga klyftan mellan tillverkning i laboratorieskala och produktion av stora volymer av elektroniska enheter baserade på tvådimensionella material, Graphene Flagship 2D Experimental Pilot Line (2D-EPL).
– Den här artikeln är ett bra exempel på det arbete som vi utför inom 2D-EPL-projektet, säger Cedric Huyghebaert, program manager for exploratory materials and module integration vid imec och teknisk ledare för 2D-EPL-projektet.
– Det här är en av våra mest angelägna uppgifter just nu. Att utveckla verktygslådor och designhandböcker för tillverkning av enheter baserade på 2D-material som är kompatibla med standarderna inom halvledarindustrin. Nästa steg blir att visa potentialen hos dessa processer för att producera innovativa sensorer och optoelektroniska enheter i en pilotlina.
Referens
“Large-area integration of two-dimensional materials and their heterostructures by wafer bonding”, A. Quellmalz, X. Wang, S. Sawallich, B. Uzlu, M. Otto, S. Wagner, Z. Wang, M. Prechtl, O. Hartwig, S. Luo, G. S. Duesberg, M. C. Lemme, K. B. Gylfason, N. Roxhed, G. Stemme, and F. Niklaus, Nature Communications (2021), DOI: 10.1038/s41467-021-21136-0.